生産ラインの自動化や内製化等、改善を検討される場合はぜひ当社までご相談下さい。お客様のご要望に沿った最善のプランを提供致します。実際にお客様にて採用頂いた事例をいくつかご紹介致します。
Case1:内製化と後ラインの提案
背景:
日本で充填を行い、製品販売をするメーカー様で、容器に関しては海外にあるダイレクトブロー成形のメーカーへ委託し、空容器を輸入されていました。
日本へ容器を輸入後、メーカー様で充填を行い自社ブランド製品として販売をしていました。
課題:
海外から輸入している容器は、穴開き(ピンホール)が多数ありました。日本で充填する際に液漏れが多々発生しており、不良率が多かった為、歩留まりが低い状態でした。
容器の品質を管理する為に、内製化を検討されました。
対象容器:
消毒液用500mL容器
提案:
ダイレクトブロー成形機を初めて導入されるお客様でしたので、まず当社の工場をご見学頂き、ダイレクトブロー成形について詳しくご説明させて頂きました。懸念事項であった容器の品質を管理する為に、成形機からリークテスターまで全自動(人手が入らない状態)で受け渡しを行い、穴開き(ピンホール)を検査するという後ラインをご提案致しました。
成形機の機種選定や後ライン、金型に至るまでお打ち合わせし、成形機導入から稼働まで二人三脚で進めてまいりました。
工場のオペレーターの皆様には、成形機の操作方法・成形に関する基本的な考えをご理解頂く為に、成形機完成後に当社へお越し頂き、1週間成形機の研修を受けて頂きました。
結果:
成形機と、それぞれの後ライン機器は無事納入され、納入後すぐに問題無く生産を開始されました。課題であったボトルの穴開き(ピンホール)等の不良品は殆ど無く、歩留まりが高くなりました。全てのボトルをリークテスターで正確に検査している為、万が一穴開き(ピンホール)が発生したとしても充填前にラインから外す事が出来、生産効率が上がりました。
担当営業のコメント:
品質が安定して成形出来る事でお客様からお褒めの言葉を頂きました。容器の品質が向上する事で製品の外観も良くなり、エンドユーザーが手に取る機会も増えるのではと考えます。
日本で充填を行い、製品販売をするメーカー様で、容器に関しては海外にあるダイレクトブロー成形のメーカーへ委託し、空容器を輸入されていました。
日本へ容器を輸入後、メーカー様で充填を行い自社ブランド製品として販売をしていました。
課題:
海外から輸入している容器は、穴開き(ピンホール)が多数ありました。日本で充填する際に液漏れが多々発生しており、不良率が多かった為、歩留まりが低い状態でした。
容器の品質を管理する為に、内製化を検討されました。
対象容器:
消毒液用500mL容器
提案:
ダイレクトブロー成形機を初めて導入されるお客様でしたので、まず当社の工場をご見学頂き、ダイレクトブロー成形について詳しくご説明させて頂きました。懸念事項であった容器の品質を管理する為に、成形機からリークテスターまで全自動(人手が入らない状態)で受け渡しを行い、穴開き(ピンホール)を検査するという後ラインをご提案致しました。
成形機の機種選定や後ライン、金型に至るまでお打ち合わせし、成形機導入から稼働まで二人三脚で進めてまいりました。
工場のオペレーターの皆様には、成形機の操作方法・成形に関する基本的な考えをご理解頂く為に、成形機完成後に当社へお越し頂き、1週間成形機の研修を受けて頂きました。
結果:
成形機と、それぞれの後ライン機器は無事納入され、納入後すぐに問題無く生産を開始されました。課題であったボトルの穴開き(ピンホール)等の不良品は殆ど無く、歩留まりが高くなりました。全てのボトルをリークテスターで正確に検査している為、万が一穴開き(ピンホール)が発生したとしても充填前にラインから外す事が出来、生産効率が上がりました。
担当営業のコメント:
品質が安定して成形出来る事でお客様からお褒めの言葉を頂きました。容器の品質が向上する事で製品の外観も良くなり、エンドユーザーが手に取る機会も増えるのではと考えます。
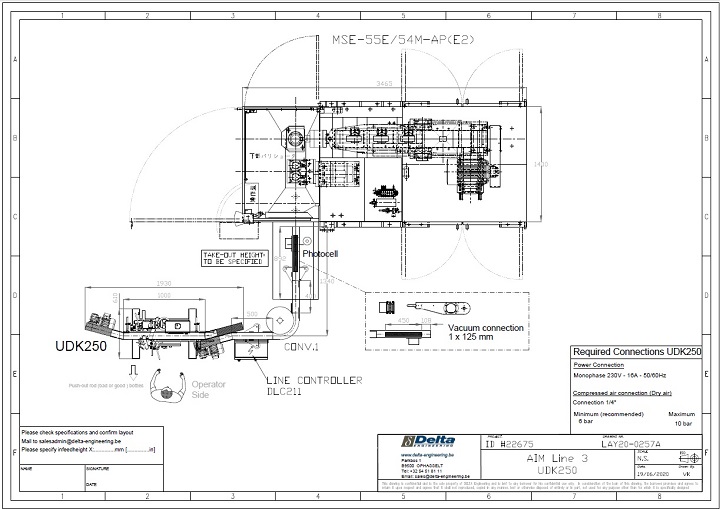
Case2:他社機からの入れ替え
背景:
中国の容器メーカー様で、日系と中華系の食品会社へ、中国製の成形機を使って成形した多層の調味料容器を納入されていました。
課題:
納入先の日系食品会社から、多層容器品質向上の改善要望を受けられました。具体的には、容器にヤケやブツが入る事や、層偏肉によるバリア性の不足が挙げられました。容器メーカー様で当時使用されていた中国製の成形機では改善に限界があった為、新規成形機への入れ替えを検討されました。
対象容器:
4種6層食品容器
提案:
当社の成形機や工場をご見学頂き、他のハイエンドの成形機メーカーとも比較検討して頂きました。他の成形機メーカーと比べて、タハラは成形機の組立だけでなく、ヘッドの流路設計や加工も一貫して自社で行っている事や、日系食品会社向けの多層容器にも実績が多くある事をご説明した結果、タハラ製の成形機を導入して頂くことになりました。
結果:
タハラ製の成形機導入後は、容器にヤケやブツが混じる事は無くなりました。また、各層の厚みが均一なボトル作ることが出来、層偏肉によるバリア性不足のトラブルも無くなりました。その結果、多層容器の受注量も順調に増えているそうです。
担当営業のコメント:
容器の不良率が大幅に下がり、お客様の信頼を得る事が出来た為、その後何台も繰り返しご注文を頂いております。当社の成形機を導入されてから、お客様が取引先から優良容器メーカーとして表彰されたお話をお聞きし、当社の成形機が良品生産に貢献出来た事を大変嬉しく思いました。
中国の容器メーカー様で、日系と中華系の食品会社へ、中国製の成形機を使って成形した多層の調味料容器を納入されていました。
課題:
納入先の日系食品会社から、多層容器品質向上の改善要望を受けられました。具体的には、容器にヤケやブツが入る事や、層偏肉によるバリア性の不足が挙げられました。容器メーカー様で当時使用されていた中国製の成形機では改善に限界があった為、新規成形機への入れ替えを検討されました。
対象容器:
4種6層食品容器
提案:
当社の成形機や工場をご見学頂き、他のハイエンドの成形機メーカーとも比較検討して頂きました。他の成形機メーカーと比べて、タハラは成形機の組立だけでなく、ヘッドの流路設計や加工も一貫して自社で行っている事や、日系食品会社向けの多層容器にも実績が多くある事をご説明した結果、タハラ製の成形機を導入して頂くことになりました。
結果:
タハラ製の成形機導入後は、容器にヤケやブツが混じる事は無くなりました。また、各層の厚みが均一なボトル作ることが出来、層偏肉によるバリア性不足のトラブルも無くなりました。その結果、多層容器の受注量も順調に増えているそうです。
担当営業のコメント:
容器の不良率が大幅に下がり、お客様の信頼を得る事が出来た為、その後何台も繰り返しご注文を頂いております。当社の成形機を導入されてから、お客様が取引先から優良容器メーカーとして表彰されたお話をお聞きし、当社の成形機が良品生産に貢献出来た事を大変嬉しく思いました。
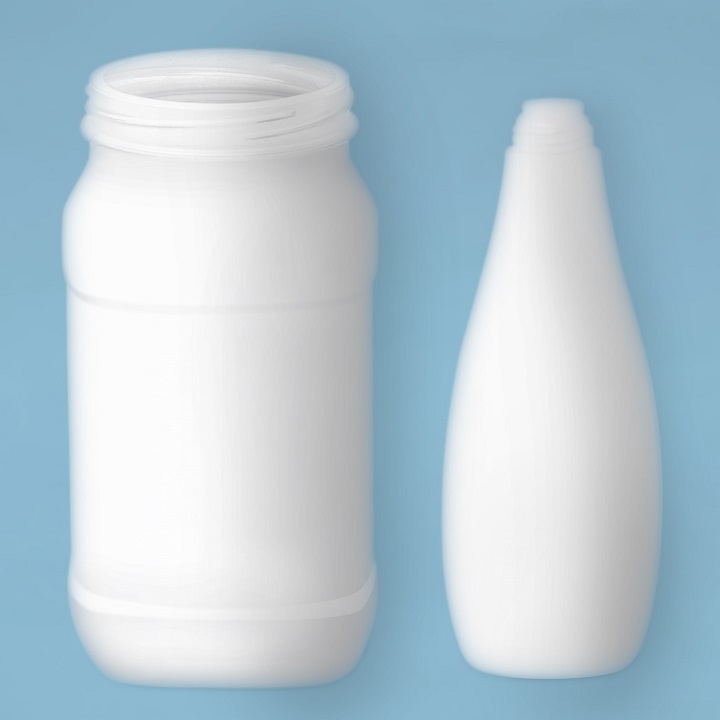
Case3:ターンキープロジェクト
背景:
外注先に大型容器の成形を依頼していた洗剤メーカー様が、空容器の輸送コスト低減を目的に容器の内製化を検討されました。
課題:
ダイレクトブロー成形機を初めて導入されるお客様なので、成形機導入前に決めて頂く事項や、成形機の他に必要な機器等をしっかり打合せする必要がありました。
対象容器:
取っ手付き大型容器
提案:
ダイレクトブロー成形に関して、成形方法や内製によるメリット・デメリットについてご説明致しました。当社の仕様書を基に、成形品に適した仕様をご提案、成形機仕様を決めていきます。成形機を導入される際は、チラーやコンプレッサー等の機械を動かす為の機器だけでなく、人手不足対応として省人化を目的に製品搬送コンベアや各種検査機器、箱詰め機等の後工程を自動化する機器を導入されるお客様が増えています。今回はチラー、コンプレッサー、エアタンク、粉砕機、コンベア、リークテスター、ウェイトチェッカー、金型を当社で一括してご提案致しました。成形機とこれらの周辺機器を、設置場所のスペースに合わせて最もコンパクトで効率の良いレイアウトで提案致しました。
結果:
当社の成形機は肉厚のバラツキが無く、動作の繰り返し位置精度も高い為、熟練オペレーターが不在でも、安定して成形する事が出来ております。また、成形後の容器の品質検査を人が行う場合は長年の経験が必要ですが、機械でチェックする事で穴あきや重量不足を確実に防ぐことが出来る上に、人件費削減にも効果的です。
担当営業のコメント:
成形機の選定から立ち上げまでしっかりとフォローし、お客様との信頼関係を構築する事が出来ました。お客様から、成形機を設置する工場建設に当たり、騒音・振動に関するご相談を受け、当社成形機の騒音・振動データを提出致しました。また、成形機導入後に樹脂変更や金型改造したが上手く成形が出来ないと相談を受けた際も、当社のサービスチームよりアドバイスさせて頂き問題を解決しました。何かお困りの事があればまず当社にご相談してください。当社の豊富な経験から最善策をご提案致します。
外注先に大型容器の成形を依頼していた洗剤メーカー様が、空容器の輸送コスト低減を目的に容器の内製化を検討されました。
課題:
ダイレクトブロー成形機を初めて導入されるお客様なので、成形機導入前に決めて頂く事項や、成形機の他に必要な機器等をしっかり打合せする必要がありました。
対象容器:
取っ手付き大型容器
提案:
ダイレクトブロー成形に関して、成形方法や内製によるメリット・デメリットについてご説明致しました。当社の仕様書を基に、成形品に適した仕様をご提案、成形機仕様を決めていきます。成形機を導入される際は、チラーやコンプレッサー等の機械を動かす為の機器だけでなく、人手不足対応として省人化を目的に製品搬送コンベアや各種検査機器、箱詰め機等の後工程を自動化する機器を導入されるお客様が増えています。今回はチラー、コンプレッサー、エアタンク、粉砕機、コンベア、リークテスター、ウェイトチェッカー、金型を当社で一括してご提案致しました。成形機とこれらの周辺機器を、設置場所のスペースに合わせて最もコンパクトで効率の良いレイアウトで提案致しました。
結果:
当社の成形機は肉厚のバラツキが無く、動作の繰り返し位置精度も高い為、熟練オペレーターが不在でも、安定して成形する事が出来ております。また、成形後の容器の品質検査を人が行う場合は長年の経験が必要ですが、機械でチェックする事で穴あきや重量不足を確実に防ぐことが出来る上に、人件費削減にも効果的です。
担当営業のコメント:
成形機の選定から立ち上げまでしっかりとフォローし、お客様との信頼関係を構築する事が出来ました。お客様から、成形機を設置する工場建設に当たり、騒音・振動に関するご相談を受け、当社成形機の騒音・振動データを提出致しました。また、成形機導入後に樹脂変更や金型改造したが上手く成形が出来ないと相談を受けた際も、当社のサービスチームよりアドバイスさせて頂き問題を解決しました。何かお困りの事があればまず当社にご相談してください。当社の豊富な経験から最善策をご提案致します。
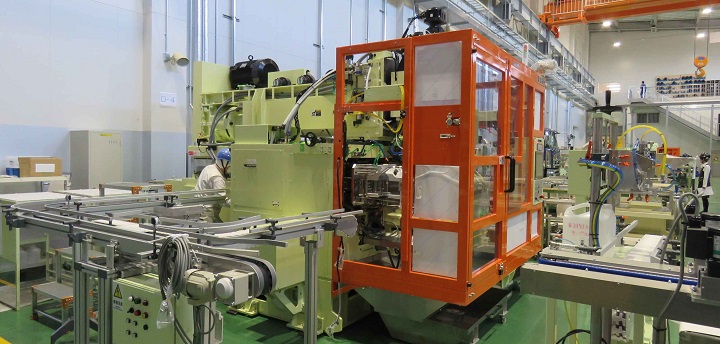
Case4:インモールドラベルの導入
背景:
東南アジアで主流の移動手段となっている二輪自動車用に、日系オイルメーカー様が自社ブランドの高級エンジンオイルの販売拡大を計画されていました。(補足:日本ではエンジンオイルは缶で販売されていますが、海外のほとんどの国ではプラスチックボトルで販売されています。)
課題:
正規のエンジンオイルを使い切った使用済み空容器に、低品質なエンジンオイルを詰めて再販される模造品が横行し、ブランドイメージの低下やクレームに苦慮されていました。
対象容器:
1Lエンジンオイル容器
提案:
ラベルメーカーとも協力し、ボトルのラベルをタックラベルからインモールドラベルに変更しました。インモールドラベルとは、金型が開いた際にラベルを金型へ貼り付け、その後金型がパリソンを掴み、エアを吹き込んで成形する際にラベルと容器が強固に張り付く仕組みです。タハラはブロー成形機とこのインモールドラベル挿入装置をセットで製造して納入しました。
そしてこのラベルは、一部のみが手で剥がせる特殊な加工がしてあり、剥がした部分の裏面をクーポンにしました。「使用済みボトルから剥がしたクーポン〇枚をお店に持っていくと、新規のエンジンオイルを1本プレゼント」という仕組みにすることで、使用済みボトルはクーポンが剥がれた状態で廃棄されます。これにより、使用済み空容器を拾い、低品質なエンジンオイルを入れて販売するという模造行為ができなくなります。
結果:
低品質なエンジンオイルを入れた模造品が大幅に減ったことで、日系オイルメーカー様のブランドイメージが高まり、二輪自動車とエンジンオイル双方の拡販に寄与することができました。
担当営業のコメント:
このプロジェクトのおかげで、タハラも成形機とインモールドラベル装置のセット販売実績が大きく増えました。インモールドラベルは洗剤容器、シャンプー容器などの分野でも幅広く活用されています。
東南アジアで主流の移動手段となっている二輪自動車用に、日系オイルメーカー様が自社ブランドの高級エンジンオイルの販売拡大を計画されていました。(補足:日本ではエンジンオイルは缶で販売されていますが、海外のほとんどの国ではプラスチックボトルで販売されています。)
課題:
正規のエンジンオイルを使い切った使用済み空容器に、低品質なエンジンオイルを詰めて再販される模造品が横行し、ブランドイメージの低下やクレームに苦慮されていました。
対象容器:
1Lエンジンオイル容器
提案:
ラベルメーカーとも協力し、ボトルのラベルをタックラベルからインモールドラベルに変更しました。インモールドラベルとは、金型が開いた際にラベルを金型へ貼り付け、その後金型がパリソンを掴み、エアを吹き込んで成形する際にラベルと容器が強固に張り付く仕組みです。タハラはブロー成形機とこのインモールドラベル挿入装置をセットで製造して納入しました。
そしてこのラベルは、一部のみが手で剥がせる特殊な加工がしてあり、剥がした部分の裏面をクーポンにしました。「使用済みボトルから剥がしたクーポン〇枚をお店に持っていくと、新規のエンジンオイルを1本プレゼント」という仕組みにすることで、使用済みボトルはクーポンが剥がれた状態で廃棄されます。これにより、使用済み空容器を拾い、低品質なエンジンオイルを入れて販売するという模造行為ができなくなります。
結果:
低品質なエンジンオイルを入れた模造品が大幅に減ったことで、日系オイルメーカー様のブランドイメージが高まり、二輪自動車とエンジンオイル双方の拡販に寄与することができました。
担当営業のコメント:
このプロジェクトのおかげで、タハラも成形機とインモールドラベル装置のセット販売実績が大きく増えました。インモールドラベルは洗剤容器、シャンプー容器などの分野でも幅広く活用されています。

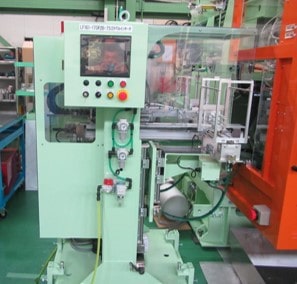