TAHARA Fully electric molding machine lets you implement sustainable business! Part 1
6/1/21
Part 1
The sustainable economy is now key issue to tackle for many companies and it will be your competitive advantage at the same time. We suggest some solutions our machine can do and hope this newsletter helps you update on the latest blow molding trend and refine your business strategies.
Reducing Food Waste
Do you know multi-layer package? Multi-layer package is that its wall consists of more than 2 layers to add functional layer, which is composed of different kind of resin. That can be made by direct blow molding machine which has the extruders for each resin and the head to combine these resins.
Common functional layers are barrier layer, recycled layer, shiny layer and view line. With this technology, you can add more value like preventing from oxidization or volatilization, adding chemical resistance, making appearance of the package attractive or reducing the amount of resin to use.
This technology could be one of solutions for reducing food loss. The package is protected from oxidation by adding barrier layer to food or seasoning multi-layer package that makes shelf-life much longer. It is often used for seasoning packages and tubes like dressing, mayonnaise and other familiar condiments which you can always see in supermarket or kitchen. Famous resins which have barrier property are EVOH and PA.
In this way, multi-layer package contributes to reduce food waste but these special resins are expensive and it comes at a big cost with using a lot of these resins. For that reason, these layers are usually only 2~3% of whole layer thickness. It’s difficult to make an equal thickness layer if this thickness is too thin. If barrier layer thickness is too thin or broken, barrier function doesn’t work perfectly.
Therefore, we suggest our Co-ex-blow molding machine. Our calculated head resin route can make equal thickness for each layer, so you can use exact amount of expensive resin as much as required. This technology requires special calculation of flow route, accumulated knowledge and elaborated assembling. Only few makers can ensure this accuracy and TAHARA is actually one of them.
In addition to that, these resins like EVOH and PA burn easily on a flow route of extruder and Co-ex head. In order to solve it, we calculate and design the most optimum resin flow route that prevents them from congestion at all point of extruder and head. Furthermore, of course every layer can be designed with preferred structure. The layer composition including ratio that you are able to request is up to 8-layer. Only TAHARA’s knowledge and experience make it possible.
Recycling Materials
It is a usual process for direct blow molding to have both chips (proper name as “flash”) and reject bottles while production. Most of the bottle suppliers crush and reuse them as a recycled material to save virgin material and total material costs. This recycled material is also called as “Regrind” and shape of regrind materials are not uniform so extrusion output would be unstable compared with using only virgin material. Therefore, regrind material is usually used with mixing with virgin material.
Regrind is used not only in single layer bottle but also in multi-layer bottle. By using regrind in outer layer and using virgin or additive-free resin in inner layer, you can avoid migration and chemical reaction between bottle and contents. We suggest sample layer compositions using regrind layer that are widely adopted and more value-added on the below chart.
Sample Layer Composition using Regrind Layer
Product | Layer | Inner | Outer | ||||
Mayonnaise | 6 | LDPE | Regrind | AD | EVOH | AD | LDPE |
Fuel Tank | 6 | HMWPE | AD | EVOH | AD | Regrind | HMWPE |
Agrichemical | 5 | PA | AD | Regrind HDPE | HDPE (view line) | ||
Shampoo | 4 | HDPE | Regrind | AD | PET-G | ||
Automobile Oil | 3 | HDPE | Regrind | HDPE |
In some case, regrind resin contain resin like EVOH, PA which is able to be burned easily. Molding with regrind material requires precisely calculated screw and resin flow route to avoid resin congestion points which sometimes cause burn.
In Automobile Market
Plastic tends to be criticized as one of the enemies of circular economy in recent years, but not always it is true. Related with CASE innovation in Automobile market, car companies have been replacing metal parts with plastic for fuel tank and filer pipe to reduce their total weight. That makes car fuel-efficient and it improves driving performance.
A Plastic fuel tank is made by multi-layer and some of barrier layers like EVOH and PA will be added to prevent volatilization. A Plastic filler pipe is also formed by multi-layer and filler resin will be added to give durability.
The picture below is a drive shaft boot. It’s made by our fully electric injection blow molding machine. Neck part is molded by injection molding & body part is molded by blow molding. Injection molding realizes a required precise shape and fills a tolerance of neck part, and blow molding enables to control the thickness at any point of the body part even it has complicated shape like these bellows. Major material is Elastomer resin and it was spotted on the ability of elasticity.
Drive shaft boot
Fully electric injection blow molding machine (HPS)
You can find further information on our website.
http://www.tahara-mc.com/en
Hot topic!
We just renewed our website since February 2021. You will find more contents and it became easier to get information more quickly. We added much more interesting contents like “products which can be made by our machine”, “what direct blow molding is”, “our machine range” and so on. We would recommend expanding your future possibility with our website.
Please take a look and find blow molding machine you need from below link.
http://www.tahara-mc.com/en/
Here is another news. We relocated our factory from Tokyo to Chiba in May 2019. Our factory became 3 times bigger than previous factory.
New factory also allows us to be able to assemble more efficiently. Our maximum assembling capacity per year became around 100 machines.
The location is relatively close to Narita Airport so you can easily stop by when you come to Japan.
We always welcome your visit to show our cleaner & more functional factory.
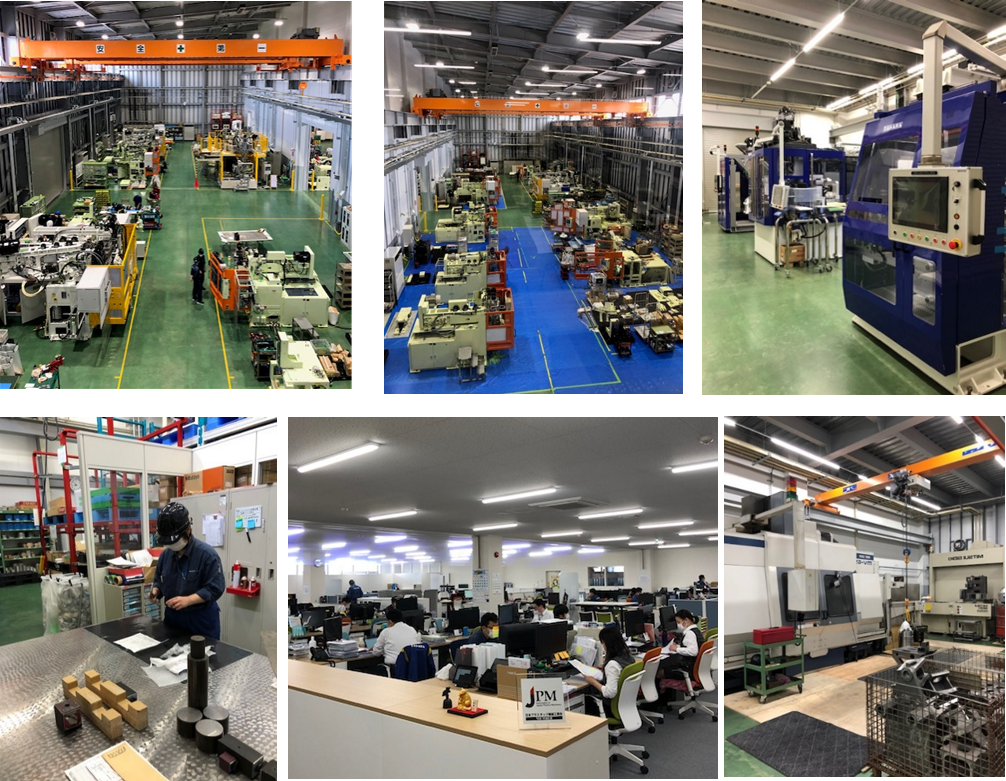
For further information, please feel free to contact us. TAHARA MACHINERY LTD. 2-1 Kaguro-Minami Inzai Chiba 270-1369 Japan https://www.tahara-mc.com/en/contact https://www.linkedin.com/company/tahara-machinery-ltd |